How HOERBIGER is embracing digitalization
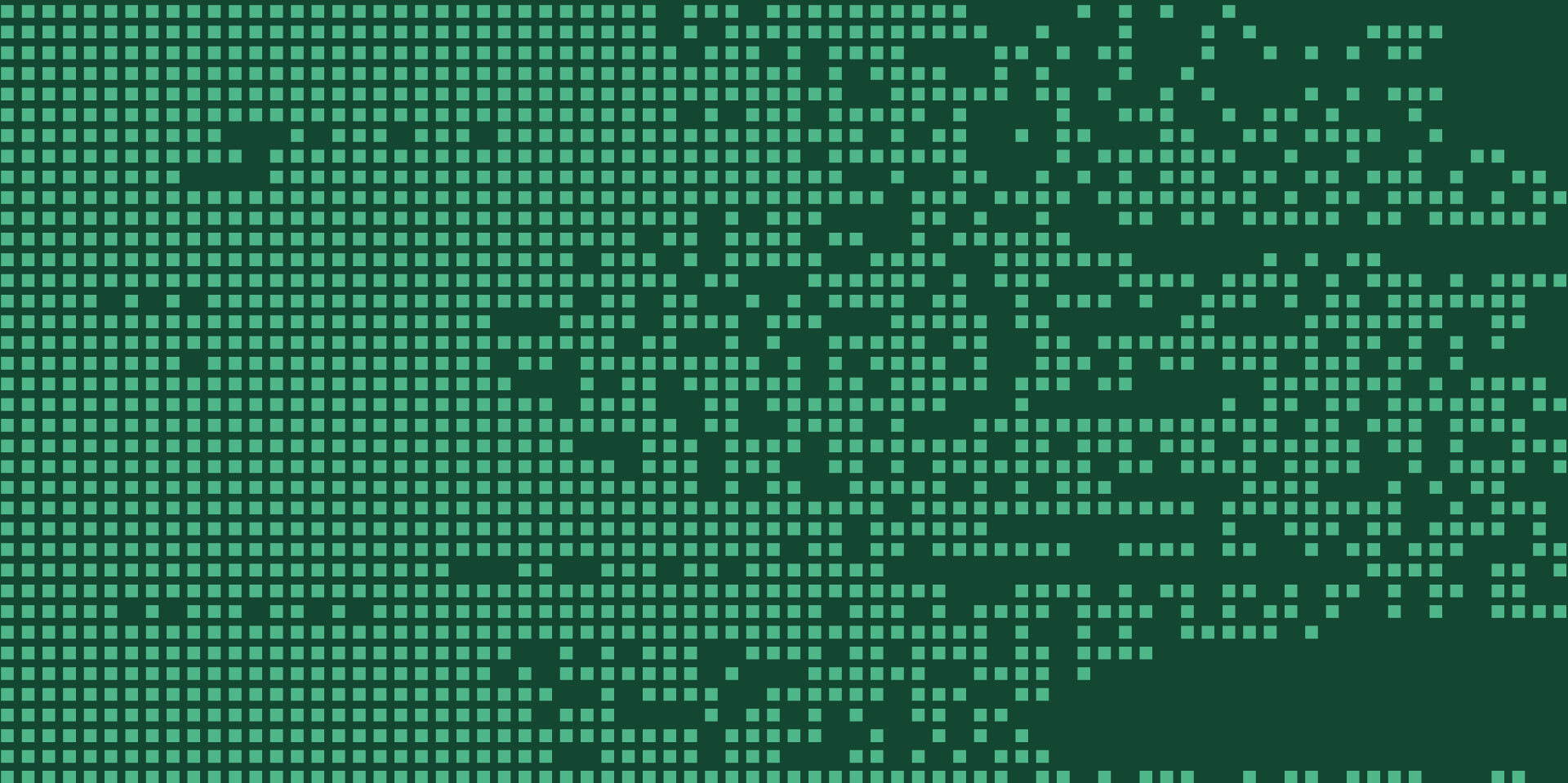
Digitalization means change, transformation, and the ability to face the challenges of our time. Its beginnings date back to a time when the best supercomputers had less processing power than a modern pocket calculator. With the advent of the internet, it became possible to share information and data worldwide. Today, digitalization is omnipresent – it permeates the economy, education, and our everyday lives.
Mechanical engineering meets megabytes
The industrial revolution has reached a new dimension with digitalization. Companies are relying on digital twins, machine learning, and automated systems to make processes more efficient, flexible, and sustainable. Artificial intelligence (AI) enables machines not only to execute commands, but also to learn independently, recognize patterns, and continuously improve themselves. Following the steam engine, the moving assembly line and information technology, the fourth industrial revolution (known as “Industry 4.0”) embraces networking and the merging of the digital and physical worlds.
To illustrate the scale of this progress: 66 years passed between the Wright brothers’ first flights in 1903 and the moon landing in 1969 – a breathtaking technological development. The time span is even greater from the first vacuum tube computer in the 1940s to today’s generative artificial intelligence, which can speak, write texts, generate images, and perform complex data analyses independently. The complexity of digital systems exceeds that of manned space flight: While the journey to the moon required reliable technology and precise calculations, modern AI demands a deep understanding of huge amounts of data, the ability to recognize patterns, and autonomous decision-making processes.*
*This text was written with AI support.
The future is now
At HOERBIGER, digitalization is not a distant utopia, but a reality – not as an end in itself, but as a means of bringing people, machines, and data into harmony. Intelligent production systems, AI-supported quality assurance, virtual simulations, and a modern work culture are part of everyday life. Digitalization is not a goal, but a process of continuous learning, application, and optimization.
The focus is not on “the big leap”, but on the precision and quality of implementation. Digitalization at HOERBIGER is guided by the principle of carefully addressing complex challenges and developing solutions that will stand the test of time. At HOERBIGER, digitalization does not mean simply replacing the old with the new, but rather connecting processes, people, and technologies in a meaningful way.
The facets of digitalization at HOERBIGER
“Thanks to digitalization, our components can be produced with even fewer errors, greater precision, and in a more sustainable and competitive manner,” says Dr. Bernhard Spiegl, CTO and Head of Innovation & Technology, HOERBIGER Group. “Digitalization is not a substitute for people, but rather a support that helps reduce routine and stressful tasks and creates more room for creativity and strategic action. However, it does transform the way people, data, and machines work together and how we succeed as a company.” At HOERBIGER, the digital transformation can be summarized in six key dimensions that together form a comprehensive digital ecosystem.
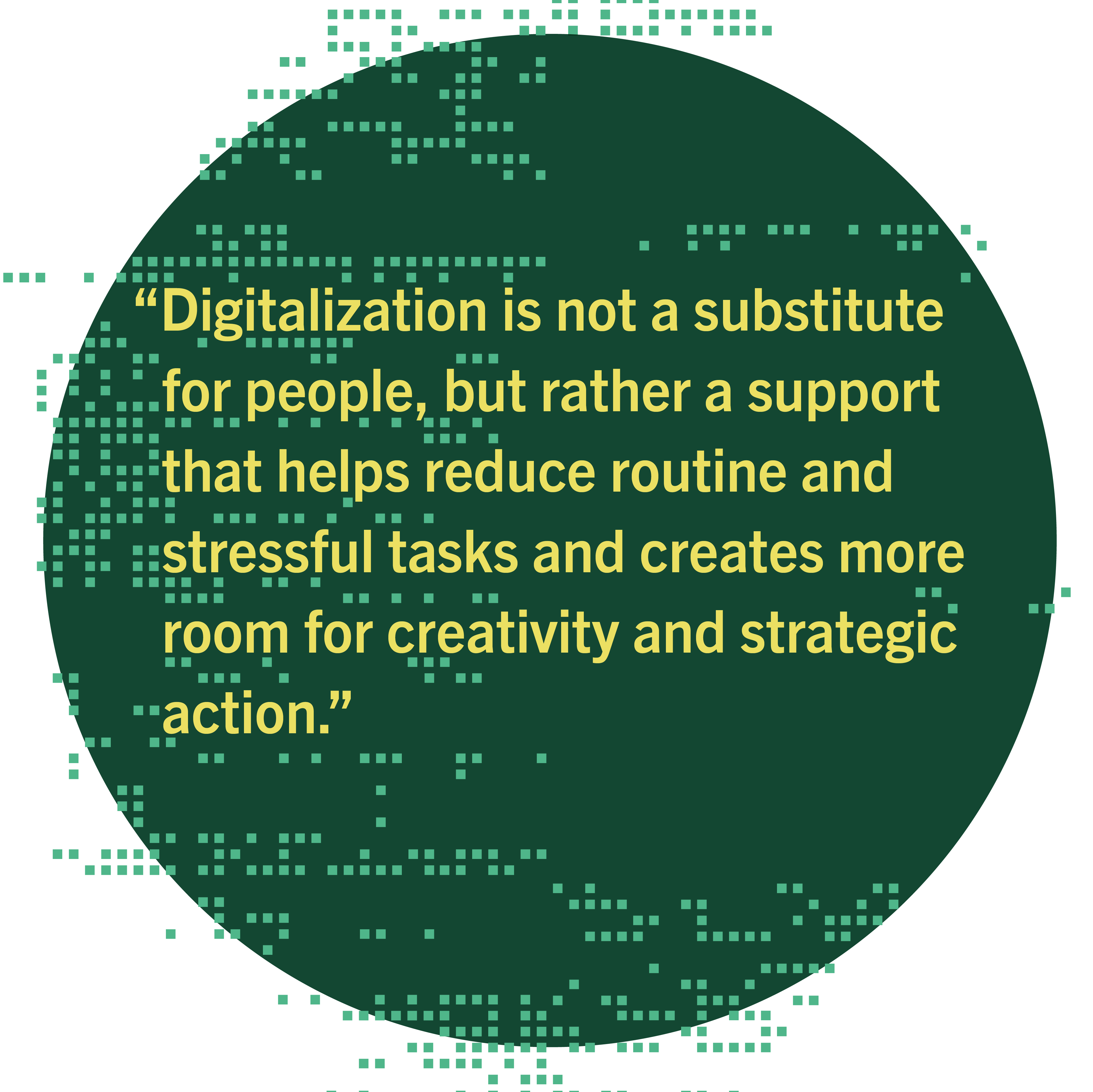
1. Integrated production
In manufacturing, digitalization means that machines and systems are interlinked. HOERBIGER relies on comprehensive digital shop floor management based on real-time data in its plants. These smart manufacturing systems use advanced data analytics to enable continuous monitoring and optimization of production processes. This significantly reduces production downtime and further improves the quality of the manufactured products. Machines are equipped with sensors that provide information on performance, status, and material consumption. Deviations from the target state are immediately detected, visualized, and employees can respond directly. At the automotive plant in Changzhou (China), driverless transport systems (AGVs – automated guided vehicles) transport materials autonomously, coordinated by a manufacturing execution system (MES) that controls and monitors the processes.
2. New business models
The development of digital solutions for customer use enables entirely new business models that intelligently expand the product and service portfolio and supplement it with digital touchpoints. The Compression Division is already using VISTRA®, an innovative digital solution, to simplify maintenance processes and increase transparency regarding the condition of compressor components. VISTRA® enables the digital recording and management of maintenance data in real time, including the history of each component, documented work steps, and replacement parts installed. In addition, the integration of real-time and historical data from production and maintenance opens up new perspectives such as intelligent analyses and automated recommendations for action that identify potential failure risks, recognize trends, and suggest proactive measures before unplanned downtime occurs.
The vision goes beyond individual solutions: “HOERBIGER is working to develop a fully integrated digital platform that seamlessly connects maintenance, data analysis, and recommendations for action,” says Dr. Gunther Machu, Head of New Ventures and Digitalization, Compression Division. “We are creating a comprehensive smart maintenance and performance management platform with the potential to fundamentally change the standards in compressor technology.” Such digital enhancements also form the basis for new business models that include data-driven services and customer solutions. These solutions are based on predictive maintenance, performance optimization, and improved availability – always with the goal of maximizing customer value while increasing operational efficiency.
“We are creating a comprehensive smart maintenance and performance management platform with the potential to fundamentally change the standards in compressor technology.”
Compression Division
3. Automation and artificial intelligence
“In the automotive sector, with its extremely high demands on quality and competitive costs, HOERBIGER consistently focuses on automation and digitalization in combination with AI,” emphasizes Andreas Veit, COO and Head of Operations, Automotive Division. This starts with simple, rule-based systems that automate defined processes and extends to statistical models and deep learning with generative AI that independently recognizes patterns, learns, and develops solutions. In quality assurance, for example, the Forced Quality Check system automatically stops production if qualityrelated tests have not been carried out correctly or on time. Production is only released after successful testing, which increases traceability, confidence in quality, and efficiency.
Guided Start of Production Acceptance ensures that production machines can only start up once the initial part inspection has confirmed that quality standards have been met. This enables HOERBIGER to reduce the proportion of defective products to a minimum with the aim of achieving a zero-defect strategy. The Predictive Tool Monitoring initiative goes one step further: by analyzing sensor data and applying machine learning, AI will in future be able to detect impending tool failures at an early stage, predict the remaining service life, and take proactive measures. This leads to a drastic reduction in waste, reduces plant downtime, and also extends machine life through early detection of anomalies in the process.
“In the automotive sector HOERBIGER consistently focuses on automation and digitalization in combination with AI.”
Automotive Division
4. Data management and traceability
Data management at HOERBIGER goes far beyond simply collecting and storing information. It is the foundation for transparency, efficiency, and quality – from the first step of manufacturing to delivery to the customer. Serialization, for example, ensures that each component receives a unique identifier that enables complete documentation throughout the entire production and supply chain. This means that it is possible to trace at any time where a part was manufactured, which materials and tools were used, and which tests it has undergone. This comprehensive traceability is crucial for quality assurance, the precise handling of complaints, and compliance with legal requirements.
But at HOERBIGER, data management means more than just traceability; it also means the intelligent use of data. Modern analysis and visualization technologies such as Process Mining make complex production and business processes transparent, identify bottlenecks, and improve workflows. These insights are then fed back into production planning, quality management, and product development. In the future, even closer integration of data management with digital systems such as maintenance and quality data is planned to create a complete digital mirror image of production reality.
5. Simulations and virtual tests
Simulations and virtual tests are a key factor in product development at HOERBIGER. Powerful simulation tools are used right from the design phase to test and optimize complex components and systems virtually. This allows critical influencing factors to be identified and the best design solutions to be developed – even before the first physical prototype is built. This saves time and money, minimizes the risk of design errors, and significantly improves product quality. “A specific example is the transformation of classic mechanical shift systems into electromagnetic actuators,” says Dr. Ansgar Damm, Head of Research & Development, Automotive Division. “Through comprehensive simulation of component behavior, manufacturing tolerances, and load scenarios, we can develop robust, durable, and efficient products that meet HOERBIGER’s high quality standards.”
“Through comprehensive simulation of component behavior, manufacturing tolerances, and load scenarios, we can develop robust, durable, and efficient products.”
Automotive Division
6. Modern Work and collaboration
Digitalization is changing not only business models and production processes, but also the way people work at HOERBIGER. “With the introduction of Microsoft Copilot, artificial intelligence is finding its way into everyday office life,” says Thomas Kriechbaum, CPO and Head of Process Management & IT, HOERBIGER Group. “Copilot supports employees in creating documents, analyses, and summaries, opening up space for more efficient and creative work.” The new social intranet MyHoerbiger is the digital home for all employees. Here they can find company news, knowledge, and social interaction. It connects employees worldwide and promotes a corporate culture based on openness, transparency, and collaboration. Supplemented by Microsoft Teams and SharePoint, cross-location collaboration becomes the norm – whether in the office, working from home, or in the field. HOERBIGER embraces modern ways of working and shows how technology and culture go hand in hand.
Another building block of the modern working world at HOERBIGER is the use of SuccessFactors. This cloud-based Human Experience Management (HXM) suite supports the company in all People & Culture processes – from recruiting and onboarding to employee development, target setting, and succession planning – enabling a holistic and integrated view of career paths. Particularly noteworthy is the ability to automate processes through self-service and give employees and managers more responsibility.
“With the introduction of Microsoft Copilot, artificial intelligence is finding its way into everyday office life.”
HOERBIGER Group
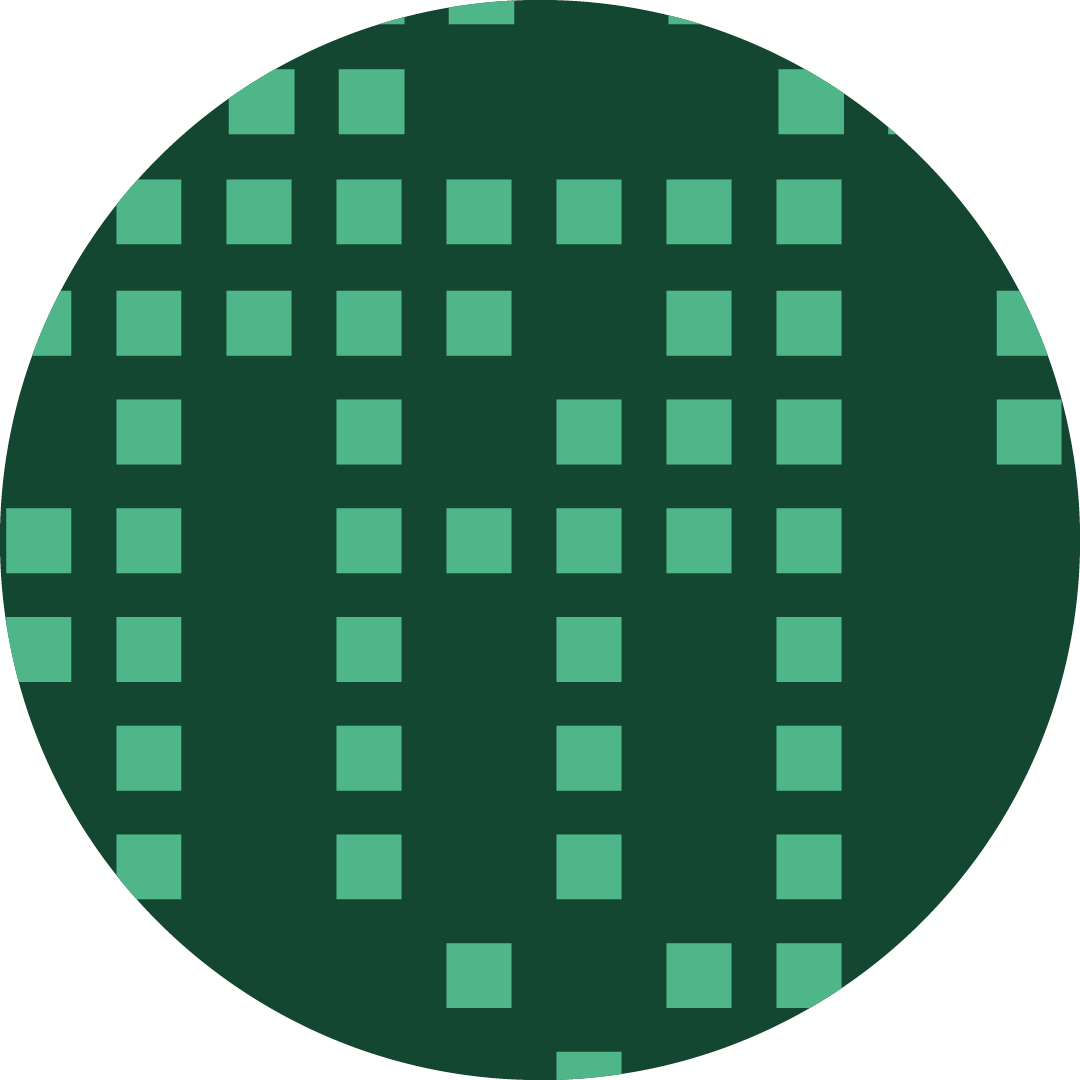
Cybersecurity in the digital world
Cybersecurity is the foundation of every successful digitalization. It encompasses not only the protection of IT infrastructure through firewalls, virus protection, and secure networks, but also monitoring and incident response services that sound the alarm in the event of suspicious activity and initiate countermeasures. Nevertheless, people remain at the heart of the matter: Only through targeted training, awareness-raising, and clear rules of conduct can companies ensure that employees recognize risks and behave responsibly. At HOERBIGER, people are therefore at the center of the IT security strategy – because no technology is more secure than the knowledge and awareness of the people who use it.